Table of Content
Here’s a step–by–step overview of the manufacturing process from the mobile home framing, to the flooring and exterior walls, all the way to the delivery stage. Ideally, they were referred to as “trailer homes,” which were less expensive structures made to address the housing demand after World War II. With properties, we find for more stick-built homes that suffer from functional obsolescence than mobile homes. One of the reasons is that homebuyers typically have much higher expectations for a stick-built home.

We want to shine a light for you on this aspect of manufactured housing by providing you with a bottom-to-top breakdown of the typical mobile home. Purchasing a new manufactured home is very different from the process of buying a motor vehicle. There are a lot more moving parts, which can be confusing. Animals quickly discover holes in skirting and enter the crawl space to nest or scavenge for materials. Also, moisture can easily enter the crawl space under the home through gaps in the skirting. Then, take 1 x 2 lumber and screw it securely into the floor joists over the plastic sheeting where the new wrap overlaps the old wrap.
Ways To Remodel A Mobile Home To Make It Look Like A House
Ceiling materials, is far easier to repair than warped or rotted trusses. PROBLEM – If leaks are not repaired, wood rot can occur rapidly. Remember, that the rot that occurs is in the actual structure of the home.
SOLUTIONS – If the piers are metal and rusted badly they should probably be replaced. If they are cement piers or cinder blocks, check to make sure that they are still straight vertically. If they have tilted, chances are the foundation they are sitting on has begun to sink. If this is the case, they will need to be removed, and the cement footing replaced or repaired. The piers can then be reinstalled and shims used to level it out.
What Materials Are Mobile Homes Made Of?
This is mainly because manufactured homes do not use bricks, mortar or cement in the construction. The actual materials used in both types of homes tends to be the same. When the HUD building standards for manufactured homes was put into place in 1976 it created a uniform construction code that all manufactured homes must adhere to. This code has continued to be improved over the years; such as fire resistance, plumbing, wind resistance improvements and more have made the homes sturdier over the years.
PB pipes in a mobile or manufactured home are often gray, and you may find them around the water heaters, sinks, toilets, and shut-off valves. The only remedy for a mobile home with PB pipes is to replace them all, which can cost several thousand dollars. Looking to buy a mobile home, but not sure what make and model to choose?
How Mobile Home Walls are Built in Manufactured Homes
They also don’t waste a lot of time tacking wire to the studs inside the walls. So if you work where you are not on a direct line between a wall switch and a factory installed ceiling fixture you are probably OK. The safe weighs 500 pounds and will end up being 600 pounds fully loaded. I have located where one of the center beams runs and will locate the safe over the beam near the middle of the trailor. We have a very large collection of books that are placed in teak bookcases which are also very heavy.
PROBLEMS – Over time, the shingles will succumb to the weather. When this happens, they are no longer able to seal out the water and will often leak. Often, the quick fix is to jack up the home just a bit and install wood shims to regain the support.
Manufactured home construction
This is usually one of the first things new owners upgrade. This opportunity is also usually used to add a small welcoming patio to the front of the home. The typical mobile home is still distinguishable from a traditional stick-built home.
Department of Housing and Urban Development’s Manufactured Home Construction and Safer Standards code. The CFPB believes that the term “mobile homes” as used in the Census and Census Pulse survey likely captures the majority of manufactured homes. About the same time, we purchased another 12 x 60 mobile home on a good lot that was a 1968 model. It had not been maintained and was in such a condition that is was strictly a tear down. As we were having the home torn down, I was looking closely at the construction quality of the homes. The flooring was actually 1 inch thick plywood over steel beam girders (there weren’t any floor joists between the subfloor and the frame).
I’m sure that with the proper support in the ceiling and possibly some extra support under the home it can be done. However, I never messed with load bearing walls and can’t offer any specific suggestions. Was working with 7′ ceilings with wall support at 9′ and 6′ and 8′ support of the 24′ 2×4.
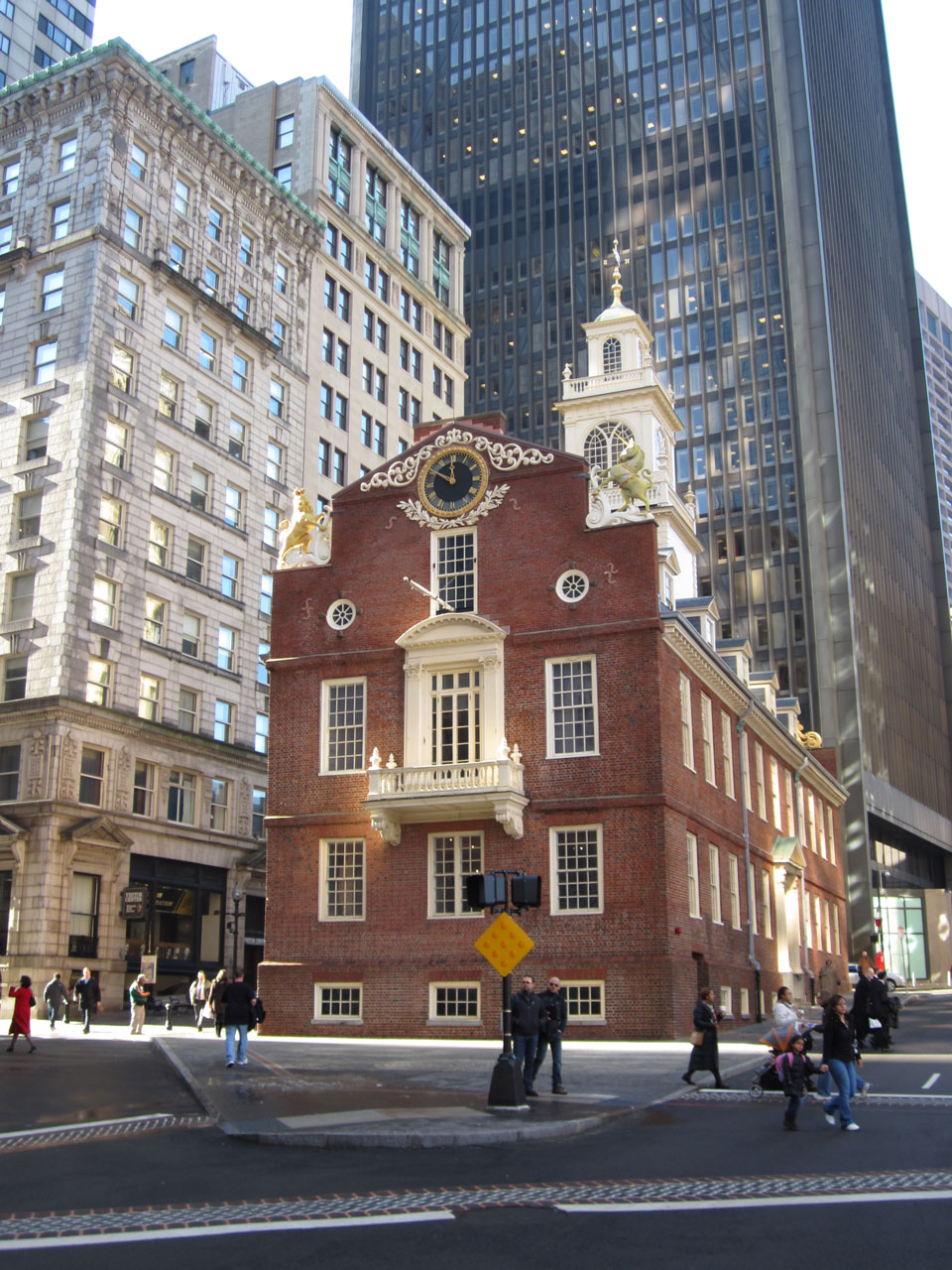
Mold also becomes a major issue with the ground being constantly wet. Repair any missing insulation and belly-wrap underneath the home. This can be done by taking new plastic sheeting and spreading it over a much larger area than the damaged part.
The quality of the materials used tends to have a lot to do with how long the homes will last. "Every time there's a hurricane we see a number of our older homes that suffer catastrophic failures," says Jim Ayotte, CEO of the Florida Manufactured Housing Association. "The pressure on affordable housing in Florida is just excruciating," says Gladys Cook, director of Resilience and Disaster Recovery at the Florida Housing Coalition. "We've had land costs and construction costs go up 30 percent in just the last couple of years." • Prepare the Interior – You need to ensure that all the components in a home’s interior that can be shaken loose are either removed or fixed firmly. The closet, light fixtures, cabinet doors, toilet tank tops, and so many other components need to be secured tightly.
No comments:
Post a Comment